Healthcare for Your Facilities
BY DAVID S. OSBORN, JD |
Healthcare for your facilities Developing and maintaining a care plan for your facilities and equipment is critically important to organizational value |
The quality of healthcare does not stop with your residents; it extends to the facilities housing them. While long-term healthcare organizations take great pains to identify and use the latest systems to monitor the health of their resident-patients, little has changed over the years in the practice of monitoring and maintaining the health of their portfolio facilities. This attitude ignores the balance sheet. A quick look at the 2004 financial statements of six large U.S. public long-term care chains reveals that on average, more than 50% of their overall market capitalization lies in their property, plant, and equipment-far too large a percentage to ignore.1 The care and feeding of your physical assets is as critical to organizational value as the healthcare provided to the human assets comprising your customer base. Both require your full attention and an equal commitment. This article will help you gauge your facility care plan and suggest new ways to improve it. The Price of Poor Maintenance Minor facility-related incidents resulting from improper facility conditions such as slip and fall accidents, intruder-related injuries, and injuries resulting from inoperable or poorly maintained equipment may not make your blood chill, but your bottom line may limp for years to come. Simple accidents can cause serious injury and can lead to more than minor cuts and bruises for those who land on hard surfaces and suffer fractures and strains. Consider a $2.8-million verdict collected by a guest who tripped near the threshold of a nursing home and permanently injured his back; a $210,000 award to a nursing home resident who fell and broke her hip because of an improperly maintained walker; a $175,000 award to a woman who injured her foot when the facility permitted a manual door to remain in an unsafe condition; a $70,000 recovery when a plaintiff slipped and fell on a chronic wet spot; and a $210,000 award when a nurse was injured because the nursing home had negligently failed to repair a long-standing pothole in the parking lot. The fundamental question underlying a cause of action related to your facility or equipment (premises liability) is whether the condition causing the accident was unreasonably dangerous and could have been avoided. Premises liability is a broad legal term that denotes many types of events relating to your building and grounds, including structural design flaws, unsafe physical conditions, environmental hazards, improperly maintained equipment, improper movement patterns, and a range of other issues involving negligence. According to a 1998 report by Jury Verdict Research, The 5 Myths of Nursing Home Litigation, premises liability accounts for 8% of all long-term care liability cases. Furthermore, plaintiffs have a recovery probability of over 50% in nursing home cases compared with approximately 30% for medical malpractice cases. The median verdict for nursing home negligence approaches $200,000 and can rise to $13 million when the verdict includes compensatory damages. Punitive damage awards accompanied 19% of all plaintiff verdicts with a median award of $900,000. Beyond liability and risk is diminished facility value borne out of improper maintenance. When it comes time to borrow cash, to sell your facility, or to market your services to new clients, facility condition is an integral component of the audience’s perceived value. Consider how a complete record of facility maintenance would add to a buyer’s or a client’s positive perception of care. Simply having equipment data at your fingertips will save you money. One recently acquired organization with an Internet-based preventive maintenance system in place saved considerable time, effort, and expense when its acquirer asked for an inventory of current assets. Fortunately, a complete list of facility equipment, its current condition and, therefore, its approximate value was only a few clicks away. Programmed Preventive Maintenance In a recent report prepared by Jones Lang LaSalle,2 the authors quantified the return on investment (ROI) to be realized by an organization that performs preventive maintenance (PM) on its major building systems in real market conditions. By comparing the usable life, energy efficiency, and repair costs on properly maintained building systems against these same criteria for building systems where no preventive maintenance was performed, the authors’ overall conclusion was “overwhelmingly positive for performing preventive maintenance.” Their analysis demonstrated “that an investment in PM not only pays for itself but also produces a huge return on the investment.” Experiencing a return on investment of 545% for the tested equipment, they determined that the bulk of the return comes from increasing its useful life. They concluded that “the longer the capital expense can be delayed, the higher the ROI.” In short, properly maintaining all the equipment in your portfolio produces a significant return. The report offers a powerful argument for the value of maintaining a comprehensive preventive maintenance program and the dramatic impact it can have on the value of your real estate investments. Tenets of Program Success So where do you begin? Start by objectively evaluating your current maintenance practices. Ask a few simple questions. Do I know what equipment I have on-site? What percentage of my maintenance staff’s time is devoted to reactive maintenance? What does my maintenance staff do each day? What are they doing today? What needs to be fixed…the most? If you can’t easily answer these important questions, then you need to revamp your program. A well-designed program includes:
A centralized communications application will help you to begin the important process of collecting maintenance data in one central repository. The same application will enable you to share these data with affected building constituents. When you combine and standardize data collection and communications into a single program and reinforce use, you will see immediate benefits in reporting, trend recognition, communications, response times, predictability, equipment uptime, and an increased quality of resident care, which is your ultimate goal. Many types of data will comprise the central repository: Output data. Generated by the system, these include preventive maintenance tasks that detail the steps to be performed on a particular piece of equipment, and the tools and materials the technician would need to bring to the job site. These are kept in both standard (BOMA) and customized libraries within the system. Input data. These are generated by the maintenance collection and include time, materials, special conditions, observations, and readings. Input data include:
A well-designed preventive maintenance program with excellent supporting systems will save you the time and cost associated with excessive repairs only if properly and thoroughly carried out. Management leadership is critical to achieving the highest return on your facility maintenance efforts and investment. You must decide that putting a comprehensive maintenance program and supporting system in place is necessary for the efficient operation of your facilities and then convey that clearly and firmly to your maintenance staff. You must reinforce program compliance and system use. If you deploy it without management commitment and a willingness to make changes, the program will absolutely fail. You must tie dedicated usage of the system to performance reviews. You must set expectations and performance goals and make sure that they are met. If you do not take these core steps, staff will be slow to respond and your facility maintenance plan will suffer. So, too, will the ultimate level of resident care. A maintenance program generally has two operative components: service requests and preventive maintenance tasks. Both pertain to an area of the facility (e.g., room, roof) or a piece of equipment (e.g., HVAC chiller, patient lift). Service requests. Nursing staff may observe a condition (e.g., broken wheelchair, nurse call out) and submit it as an open issue to the system. The system would instantly communicate the issue to the person charged with performing the work (maintenance, housekeeping, outside vendor) via their preferred mode of communication (phone, e-mail, fax, SMS message). Importantly, the issue would remain open until the work is completed and be closed by the person with the authority to close it. If not addressed and remedied within a prescribed period (each issue type has thresholds), the issue would automatically escalate to the next person charged with overseeing that area of responsibility. Preventive maintenance tasks. The system generates daily tasks that are configured to match the staffing level at the facility and the importance of the task (i.e., is it a critical piece of equipment?). These remain open until closed by the person performing the work. The system may or may not require certain pieces of information to be entered (e.g., pressure, materials used) for the open task to be closed. Many systems (ours included) require that the technician check off tasks as they are completed so that there is a complete record. The maintenance staff would need access to a computer system with Internet access or a handheld device such as a BlackBerry or cell phone. All are becoming more prevalent in this environment. Of course, everything depends on the quality of your team. If your idea of facility maintenance is some Dickensian notion of a man in overalls in the basement, then you are in trouble. You must educate and empower your team to perform. When employees are consistently educated and given the tools to succeed, they usually rise to the occasion and deliver. Modernization and education cultivates staff loyalty, ensuring that they will stick around longer-preserving subject matter knowledge and reducing the high cost of turnover. A well-designed program supported by a flexible communications platform is an indispensable management tool and should be treated as such. It will help you to record the history of maintenance and repairs that take place at each facility. It will give you a working inventory of your equipment and help you to better plan for capital expenditures. It will help you to establish a comprehensive maintenance plan. It will make sure that important things that need to get done are completed on time and help you measure the ability and performance of your maintenance staff. Importantly, it will prevent your domain expertise and institutional knowledge from walking out the door when any maintenance employee leaves. In short, deployed and supported correctly it will give you many times your money back. Maintaining a proper care plan for your facilities and equipment can be challenging without the proper program and supporting systems in place. With such a significant percentage of your asset value at stake, you cannot afford to ignore your largest patient. Follow these simple steps and begin realizing a facility care plan that delivers:
David S. Osborn, JD, is President and CEO of Building Engines, Inc. For more information, call (866) 301-5300 or visit www.buildingengines.com. To send your comments to the author and editors, e-mail osborn0406@nursinghomesmagazine.com. References |
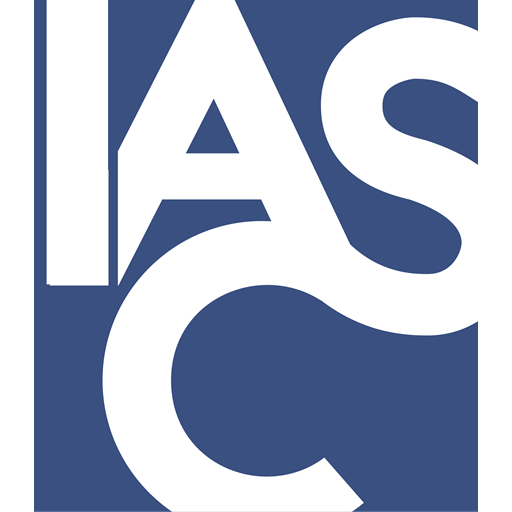
I Advance Senior Care is the industry-leading source for practical, in-depth, business-building, and resident care information for owners, executives, administrators, and directors of nursing at assisted living communities, skilled nursing facilities, post-acute facilities, and continuing care retirement communities. The I Advance Senior Care editorial team and industry experts provide market analysis, strategic direction, policy commentary, clinical best-practices, business management, and technology breakthroughs.
I Advance Senior Care is part of the Institute for the Advancement of Senior Care and published by Plain-English Health Care.
Related Articles
Topics: Articles , Facility management , Operations