Energy: Let the label be your guide
In 1992, the U.S. Environmental Protection Agency (EPA) developed the ENERGY STAR® program to promote and identify products that were energy efficient and safe for the environment. The first items tagged with the ENERGY STAR seal were computers and monitors. As the program evolved, the list of rated products continued to grow. In 1996, the Department of Energy (DOE) struck a partnership with the EPA and today-17 years later-the ENERGY STAR designation and label can be found on products ranging from light bulbs to appliances to building materials in a public-private energy-conservation effort.
EnergyGuide labels
Bearing the ENERGY STAR logo, the familiar yellow and black EnergyGuide labels are found on most energy-using products subject to minimum standards set by the federal government. Note: Items such as dryers and range/ovens are exempted from the program because they must meet minimum efficiency standards and there is currently little differentiation from model to model.
Read the label
On the left side under EnergyGuide is the description of the type of appliance and its features. The right side of the label indicates the manufacturer, the model numbers that fit the description, and its capacity.
In the information box, the estimated annual amount of energy that the particular model will use in a year is provided.
The line scale that follows shows the energy consumption estimated for models of comparable size and type.
The next paragraph gives the range of model sizes in this comparison.
At the bottom of the label is an estimate of how much this device will cost to run annually.
The EnergyGuide label, however, does have its limitations. For example, the annual operation cost will depend on whether natural gas or electricity is the energy source-it compares only costs of similarly run products. Also, when using the guide, be sure to compare similar size and models of products-if shopping for an air conditioner be sure specifications are similar and that the purchasing decision isn’t based on faulty comparison.
Yet regardless of its limitations, the EnergyGuide remains a good tool for gauging energy efficiency and costs of ENERGY STAR rated devices to rated and nonrated products.
At a glance…
Even in these challenging economic times, Americans still need to be environmentally responsible. Energy-efficient equipment and behaviors can decrease operational costs, improve the environment, and enhance your facility’s reputation.
Steven J. Kismohr, AIA, LEED AP, of GreenWorks Studio, a partner company of architectural firm Harley Ellis Devereaux, explains that the ENERGY STAR rating program enables the EPA and DOE to increase efficiency rating standards for products and practices. “Any product that receives an ENERGY STAR label,” says Kismohr, “is at least 30% more efficient than standard products.” He advises purchasers to make a conscious effort to look for the ENERGY STAR designation when selecting new or replacement equipment, comparing the equipment’s features against other like products. “Awareness is growing, especially on the coasts where energy costs are higher,” he states. Kismohr adds that conservation will play an even bigger part in equipment selection as energy prices are predicted to continue to escalate.
There are expenditures to acquiring ENERGY STAR products, explains Kismohr. “However, it’s not necessarily high-end TVs, appliances, or electronics that carry the label. Generally, it’s the more middle-of-the-road product offerings that are manufactured to conserve energy. The consumer has to research, look, and be aware,” he advises.
Becoming “green”
Lighting is the easiest “first step” in reducing energy usage and experiencing savings. “Change out the incandescent bulbs for CFLs [compact fluorescent lamps]. For larger fixtures using T12s, upgrade them to T8 and even T5 bulbs/lamps throughout the facility-indoors and out,” recommends Kismohr. “Don’t just stop at light bulbs but see if it’s possible to upgrade light fixtures to ENERGY STAR rated products to achieve additional savings, as well.”
Kismohr describes two separate sides of the equation to consider when upgrading a facility-the office side and the residential side. “On the office side, the first equipment upgrades would be the computers and monitors. There can be significant energy savings when standard monitors are replaced with flat-screen or LED monitors. If the same equipment is replaced with computers and monitors bearing the ENERGY STAR logo, up to a 90% savings can be realized. How much is that? Not a lot, probably $5 savings in the Midwest where energy costs are lower. However, if you multiply that by the number of computers and monitors throughout your organization-office, nursing, resident rooms-the amount of savings can be exponential,” explains Kismohr.
The facility side of the equation also can be retrofitted with ENERGY STAR rated products. “Foodservice operations can greatly benefit from reduced energy equipment,” says Kismohr. In that environment, steamers, dishwashers, refrigerators/freezers, ice machines, and other cooking equipment often use a lot of energy. Replacing them with energy-saving appliances can greatly decrease operational costs. “This is a great way to incrementally renovate and upgrade a facility,” adds Kismohr.
ENERGY STAR in design
For construction materials, along with energy-efficient windows and lighting, roofing products (or for a flat roof, membranes) also may be ENERGY STAR rated. Kismohr notes, “ENERGY STAR rated shingles are also available with high reflectivity quotients. Unfortunately there is currently a limited selection of these types of shingles. However, every year more manufacturers get on board to earn the ENERGY STAR rating on their products.” According to Kismohr, a reflective roof eliminates the heat gains that pass through the roof into the living space. Because the interior stays cooler, the air conditioner works less and cost savings occur with less use.
Is it time to upgrade?
Today’s technology is designed with planned obsolescence. Unlike appliances our grandparents had, modern equipment will not last for years. Why? The growing demand for “bells and whistles” on appliances and other equipment have made the inner workings far more complicated and expensive to repair. And what is state of the art in 2010, might be a dinosaur by 2011. To illustrate, Kismohr estimates that refrigerators have an approximate six-year life cycle as a result of the changes in cooling technology. “However, I believe a 10-year rule is a good yardstick to use,” he adds, “because replacement should happen once the appliance has completed its useful life.” On the other hand, if an item is serviced and repaired repeatedly, it’s time to consider investing in new equipment regardless of its age.
Steven J. Kismohr, AIA, LEED AP, at GreenWorks Studio, a partner company of Harley Ellis Devereaux, Chicago. Kismohr’s passion for sustainable design has been influenced by his work with nonprofit energy organizations and in his current role as Co-Chair of the AIAChicago Committee on the Environment (COTE).
For more information, call (312) 324-7405, e-mail sjkismohr@hedev.com, or please visit https://www.greenworksstudio.com. To send your comments to the editor, e-mail mhrehocik@iadvanceseniorcare.com.
Long-Term Living 2010 March;59(3):34-35
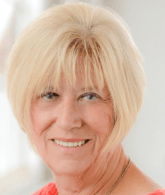
Sandra Hoban was on I Advance Senior Care / Long-Term Living’s editorial staff for 17 years. She is one of the country’s longest-serving senior care journalists. Before joining Long-Term Living, she was a member of the promotions department at Advanstar Communications. In addition to her editorial experience, Sandi has served past roles in print and broadcast advertising as a traffic and talent coordinator.
Related Articles
Topics: Articles , Facility management , Operations