Identifying hazards before an event occurs
In previous articles, I have referenced the Occupational Safety and Health Administration’s (OSHA's) National Emphasis Program on Long-Term Care (NEP) many times. Feedback I received suggests to me that I may have left some of you feeling that the areas addressed in the NEP are the only areas we need to be concerned about in developing and maintaining our safety management programs. That is not the case.
Under the OSHA Act, employers are expected to conduct a hazard assessment of the workplace to identify any occupational hazards (injury or illness) that employees may be exposed to, and take the appropriate steps to safeguard and protect employees from hazards.
To simplify the process, let us take a systematical look at a “typical” long-term care facility and identify what hazards may be present:
Resident rooms/Bathrooms:
- Biological hazards
- Electrical hazards
- Ergonomic hazards
- Fire safety hazards
- Sharps hazards
- Slip, trip and fall hazards
- Violence and aggression hazards
Gardens and grounds:
- Biological hazards
- Chemical hazards
- Environmental hazards
- Electrical hazards
- Ergonomic hazards
- Fire hazards
- Manual hazards
- Noise hazards
- Slip, trip and fall hazards
- Resident transport hazards
- Violence and aggression hazards
Hallways/Corridors:
- Electrical hazards
- Fire hazards
- Lifting hazards
- Slips, trips and fall hazards
Kitchens:
- Biological hazards
- Chemical hazards
- Electrical hazards
- Ergonomic hazards
- Fire hazards
- Heat/health hazards
- Hot surfaces/hot product/steam hazards
- Machines and equipment hazards
- Manual lifting hazards
- Natural gas/LPG hazards
- Non-ionizing radiation hazards
- Racking/stacking hazards
- Sharps hazards
- Slips, trips and falls hazards
- Walk-in refrigerators or freezer hazards
- Wet work hazards
- Working at height hazards
Laundry:
- Biological hazards
- Chemical hazards
- Electrical hazards
- Equipment hazards
- Ergonomic hazards / manual lifting
- Fire hazards
- Hot surfaces/heat hazards
- Noise hazards
- Sharps hazards
- Slips, trips and falls hazards
Lounge/Activity rooms:
- Electrical hazards
- Fire hazards
- Manual/resident handling hazards
- Slips, trips and falls hazards
Maintenance/Shop areas:
- Automobile hazards
- Biological hazards
- Chemical hazards
- Confined space hazards
- Electrical hazards
- Equipment hazards
- Fire hazards
- Lone work hazards
- Manual handling/lifting hazards
- Noise hazards
- Sharps hazards
- Slips, trips and falls hazards
- Welding hazards
- Working at height hazards
Nurses' stations:
- Biological hazards
- Chemical hazards
- Ergonomic hazards
- Electrical hazards
- Fire hazards
- Manual handling hazards
- Noise hazards
- Slips, trips and falls hazards
- Stress related hazards
- Working at height hazards
Office areas:
- Chemical hazards
- Electrical hazards
- Equipment hazards
- Ergonomic hazards
- Fire hazards
- Manual handling hazards
- Noise hazards
- Slips, trips and falls hazards
- Working at height hazards
Physical therapy/Sluice areas:
- Biological hazards
- Chemical hazards
- Electrical hazards
- Ergonomic hazards
- Falling objects hazards
- Fire hazards
- Manual handling hazards
- Slips, trips and falls hazards
- Violence and aggression hazards
My hopes are that you will share this extensive list with your safety committees and that they will use it as a guide when they are performing the required ongoing safety assessments in all areas of the facility.
When a hazard is identified, it must be corrected immediately, or else one of the following must be done:
- Initiate a repair order/work order and interim safety steps to minimize or eliminate the risk to employees.
- Make changes in work practices so that employee activities minimize or eliminate risk.
- Put in place appropriate engineering controls to minimize or eliminate the risk.
- Provide training to employees that identifies the hazards, makes the employees aware of the potential outcomes and provides methods that the employee should use in performing his duties to minimize the risk.
Recognizing and identifying hazards is the first step in reducing occupational injuries and illnesses. As we move forward, we will visit different types of work practice controls and engineering controls that you can consider or implement to manage risk.
In the meantime, stay safe and stay in touch.
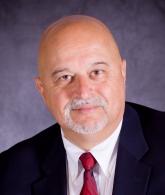
Steve Wilder, CHSP, STS, is president and chief operating officer of Sorensen, Wilder & Associates (SWA), a healthcare safety and security consulting group based in Bourbonnais, Ill. SWA performs workplace safety compliance audits and security vulnerability assessments in all types of healthcare facilities. Wilder can be reached at (800) 568-2931 or swilder@swa4safety.com.
Related Articles
Topics: Risk Management